Četrtek, 26. 9. 2013, 5.04
9 let, 2 meseca
Opel flex plant – proizvodni tempelj sodobnih, zmogljivejših in tišjih motorjev
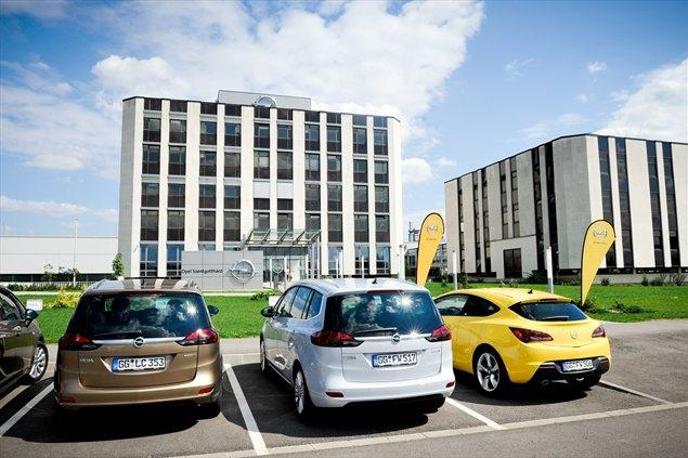
Začelo se je leta 1991
Opel je tovarno, ki se nahaja nedaleč od slovenske meje začel graditi pred dobrima dvema desetletjema. Leto kasneje pa so iz nje že začeli prihajati prvi motorji.
Med 1992 in 1999 so v tej tovarni, ki kruh med drugim reže tudi mnogim porabskim Slovencem, imeli tudi linijo na kateri so sestavljali modela astra classic in vectra.
Vseskozi pa ta Oplov proizvodnji obrat velja kot eden najpomembnejših in najbolje opremljenih templjev za izdelavo ključnih pogonskih komponent – motorjev in menjalnikov.
190 milijonov evrov vreden in 3,2 hektara velik prizidek za srednjeprostorninske bencinske in dizelske stroje
Opel nam je tokrat odprl vrata čisto novega, 190 milijonov evrov vrednega in prek 3,2 hektara velikega ter tehnološko najbolj dovršenega prizidka te velike tovarne. V njem so namreč letos pričeli izdelovati dva prva in povsem na novo zasnovana srednjeprostorninska predstavnika napovedane motorne ofenzive – 1,6-litrski bencinski turbo motor iz serije SIDI in 1,6-litrski dizelski CDTI motor. Oba smo vam tehnično sicer že predstavila v okviru prve vožnje opel zafire tourer.
Razvojni inženirji so nas tudi tokrat opomnili, naj bomo na relaciji od Dunaja od Monoštra, ki smo jo prevozili v modelih, opremljenih z novima strojema, pozorni na porabo, motorno prožnost in količino hrupa ter tresljajev.
V vseh teh postavkah namreč želijo posekati razredne konkurente. Zlasti novi dizel, 1,6 CDTI (100 kW in 320 Nm ter 16:1 kompresijsko razmerje) se je tudi tokrat izkazal kot res zelo tih in uglajen. O njem smo spregovorili tudi v tovarni, kjer so nam zatrdili, da je emisijsko povsem primerljivi z bencinskimi motorji, saj mu "blueinjecition" sistem SCR (selektivna katalitična redukcija) drastično znižuje okoljsko zelo škodljive izpuste dušikovih oksidov.
Flexplant modularna linija se je skoraj hipno zmožna odzvati na zahteve trga
Dve novi proizvodnji hali (flexplant) so s svojimi modularnimi linijami za obdelavo motornih komponent, montažo motorjev in kontrolnim procesom zasnovane tako, da se na njih brez težav hkrati izdeluje oba nova turbo motorja – bencinarja in dizla.
Znotraj ene izmene lahko tako vsaka skupina dela na bencinskem ali pa dizelskem motorju in to brez dolgotrajnih posegov v krmilne enote in strojno opremo linije. V primeru večjega naročila določene serije lahko izmenske ekipe v proizvodnem procesu po potrebi naredijo več dizlov ali pa bencinarjev, brez, da bi se v tem času proizvodnja enega ali drugega motorja ustavila.
Najnovejši liniji premoreta kar 270 povsem samodejnih in tudi krmiljenih strojnih modulov (roboti, stroji za obdelavo kovin, merilne naprave, naprave za sledljivost produktov …), ki bodo ob asistenci človeških ekip v polni zmogljivosti zmogli sestaviti 76 motorjev na uro.
Zahtevam prilagodljivosti in visoki učinkovitosti tovarne je seveda morala slediti arhitektura
Podroben pogled na tako, z visoko tehnologijo napolnjeno dvorano, pritegne relativno preprosta arhitektura. Pogled se zlepa ne zaleti v zid, statičnim in instalacijskim montažnim potrebam strežejo predvsem stebri in grede vseh dimenzij, najbolj pa v oči pade čisto ravna površina tal, ki je nikjer ne prekinjajo podzemni kanali ali več nivojska postavitev.
"V tovarni ni podzemnih enot, ker je modularna linija zasnovana tako, da se delavna postaja, ki bi se pokvarila ali pa zahtevala vzdrževanje, preprosto zamenja s pomočjo viličarjev," nam pojasni nadzorni tehnolog. Jasno, arhitektura je preprosta a izjemno funkcionalna.
Vse površine so povozne in lahko dostopne. Jaški, stopnice, različni nivoji … lahko zelo otežijo logistiko in vzdrževanje.
Zato je celotna linija spominja na nekakšen proizvodnji most, ki ga nad ravnimi tlemi nosijo kovinski podstavki. Kako zares domiselna in praktična je taka zasnova, smo se prepričali, ko smo na obhodu tovarne gledali, kako so, kot da bi se igrali s kockami, delavci finiširali linijo za proizvodnjo novega litrskega trivalnjika iz serije SIDI turbo. Tega bodo kot nov, pomemben mejnik v zgodovini tovarne začeli izdelovati v maju prihodnje leto.
Trening poligon za hitre prste
Pri sestavljanju motorjev, ki imajo seveda izjemno veliko gibljivih delov in sestavnih komponent, je kljub vsej napredni tehnologiji še vedno potrebno tudi ročno delo. Čas je denar je rek, ki še kako velja ravno v avtomobilski industriji.
Prva stvar, ki smo jo opazili v tej tovarni, je bil nekakšen mini proizvodnji obraz, kjer so bile ena zraven druge postavljene motorne makete iz vezane plošče, ki so se v razmerju 1:1 natančno ujemale z anatomsko podobo pravega motorja – karter, blok in glava. Na teh lesenih motorjih so bili nameščeni še vijaki za pritrjevanje vseh ostalih sestavnih delov – motornega računalnika, turbine, izpušnih kolektorjev, termostata …
To so trenažne makete na katerih vsak na novo zaposleni proizvodnji delavec osvoji procesno motoriko. Na tej uvodni delavni postaji človeški prsti dobijo hitrost in natančnost, ki jo tak posel zahteva. Linija pač ne sme stati, robot in človek preprosto morata ujeti ritem.
Veliko pozornosti je namenjene tudi kakovosti in sledljivosti izdelkov ter serij
Pri snovanju proizvodnega procesa flexplant so strategi veliko pozornosti namenili tudi kakovosti in pregledni sledljivosti serij vseh vgrajenih komponent kot tudi končnih izdelkov.
Vse referenčne vrednosti so na vsaki delovni postaji strogo izmerjene in preverjene s pomočjo laserskih tipal, ultrazvoka in drugih naprav ter sistemov za preverjanje kakovosti.
Še posebej so pozorni na tesnjenje in naleganje vseh treh ključnih delov vsakega motorja – stik motorne glave z blokom in stik bloka s karterjem.
Ker nič ne želijo prepustiti naključju, je vsak sestavni del motorja obeležen s svojo serijsko številko, podatkovnim čipoma ali matrično 2D-kodo.
Vse meritve posameznih serij, vse referenčne vrednosti končnih izdelkov in vsi identifikacijski podatki vgrajenih delov se shranjujejo v zgledno urejeni podatkovni bazi. Dostop do nje je v internem omrežju dostopen iz vseh kontrolnih postaj. Če bi prišlo do napake, ki bi morda sprožila celo vpoklic, imajo v tovarni natančen pregled nad serijami, dobavitelji …
Zato bi bil reakcijski čas identificiranja krivca in odprave napake nedvomno izjemno bliskovit. Jasno, saj gre za motorje, srce in dušo vsakega avtomobila.